
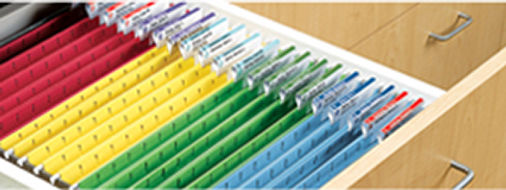
Job Summary
It was my job at Smead to design practical, accurate, easy to manufacture, low cost improvements or solutions to mechanical problems.
Responsibilities
-
Design Improvements or solutions to mechanical problems using the design process.
-
Obtain information​
-
Imagine a solution
-
Plan the best way to accomplish the solution
-
Create the idea
-
Test the idea to be sure the problem was solved
-
-
Accurate measuring and modeling of machines
-
Apply Lean Manufacturing Concepts whenever possible
-
Cooperate with others as a team in projects by asking questions and receiving input and ideas.
-
Update and create iProperties/Specs for every part to help with organization and clarity
-
Give proper names to projects according to standard naming convention
-
Create easy to read, efficient drawings with manufacturing processes in mind
-
Create bill of materials for each project that involves assembly
-
Review other drafter's work as a second opinion and a second set of eyes to catch mistakes
-
Create cover sheets for projects
-
Estimate cost of completed designs
-
Before and after pictures of projects for documentation
-
Manage files in the AutoDesk Vault
-
Create and update Internship Binder for future interns
-
Update facility drawings with any applicable changes
-
Help with planning of locations for future machines
-
Contact drafter at corporate plant when projects are complete
-
Locate engineering drawings for mechanics, machinists, and purchasing
-
Revise drawings as needed
-
Update revision tables when changes are made
-
Incorporate 3D models of commercial components into projects
-
Prepare and send out parts that can not be machined in house
-
Keep continuous contact with machinists and mechanics
-
Draw parts for mechanics and machinists as needed
-
Conduct hiring of replacement Intern
-
Conduct weekly Excel training for department
-
​
-
​
-
Example Projects
Below are some examples of projects that I have done at work. All the projects were done in either Inventor or AutoCAD. There have been a wide variety of of projects including reverse engineering, improving existing parts, creating my own solutions to problems, guarding, organization and identification of parts from drawings, updating the facility drawing, creating visuals for procedures and quality control tools and estimating the cost of my projects. For a description hover over the icon to see more details click on the thumbnail.
References
-
​Cathy Griffith - Continuous Improvement Facilitator - (435) 865-6067
-
Tony Valencia - Continuous Improvement Facilitator - (435) 865-6006
-
Josh Dimond - Engineering and CAD Intern - (435) 704-7137
-
Lori Coutts - Continuous Improvement Team Leader - (435) 865-6120
-
Ernest Burch - Lean Adviser - (435) 865-6007

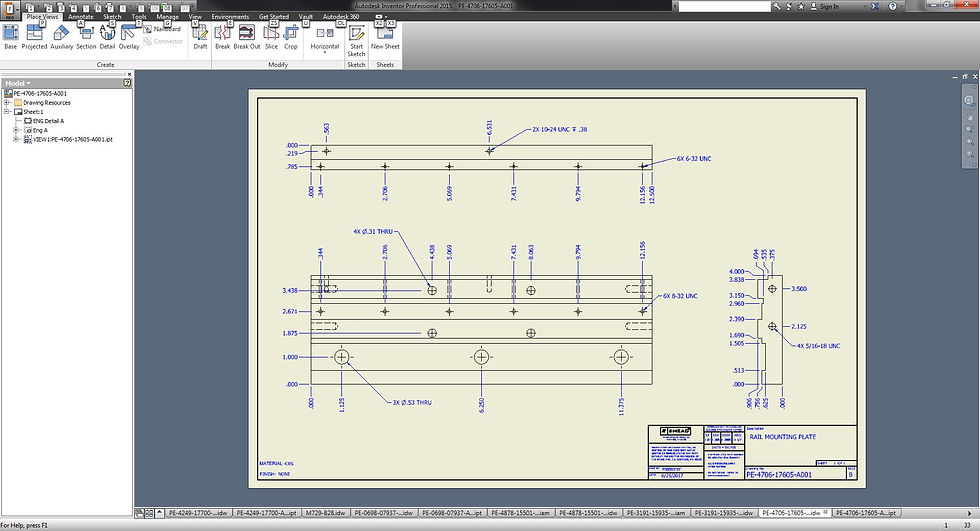
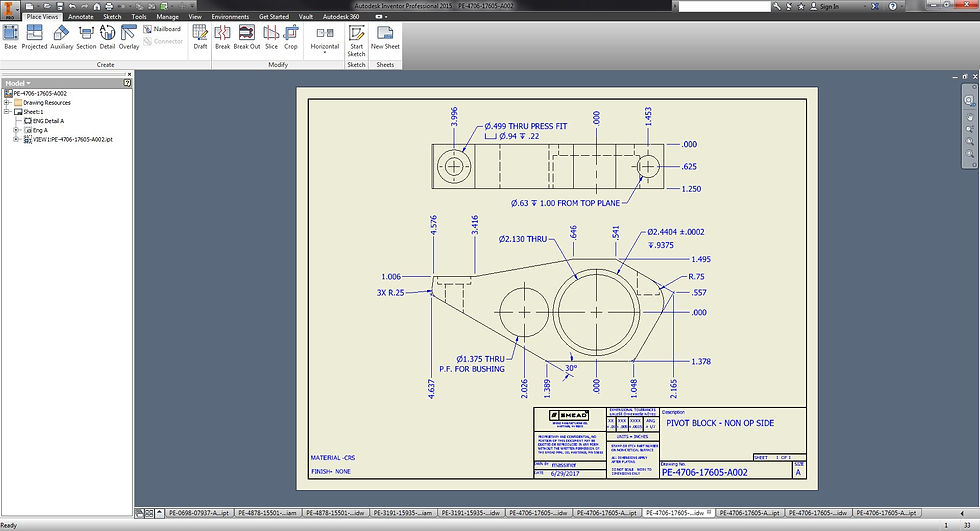

These parts were removed from a machine at our plant. The machine was purchased from another factory which had failed to include the drawings for the parts. I was handed these components to draw as accurately as possible to allow for a replacement set to be created. The replacement parts were created using these drawings and have been installed on the machine.

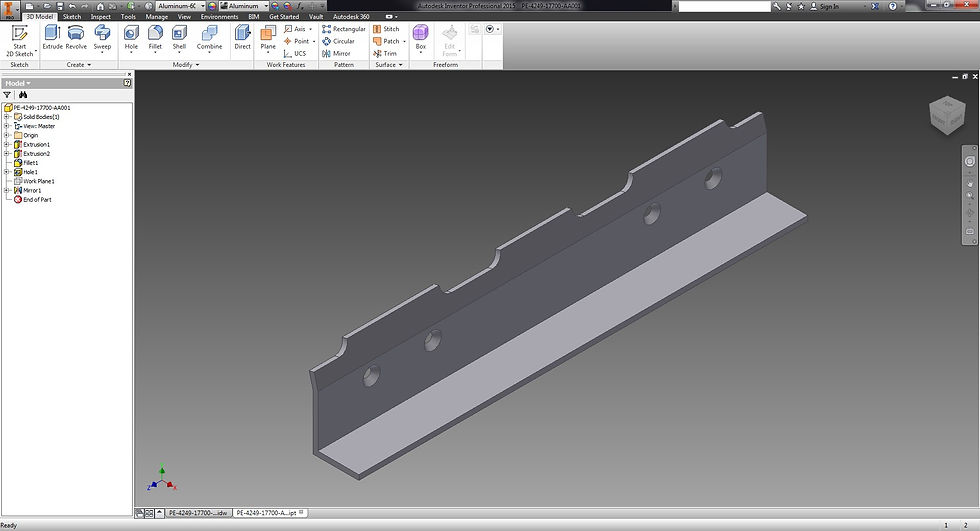
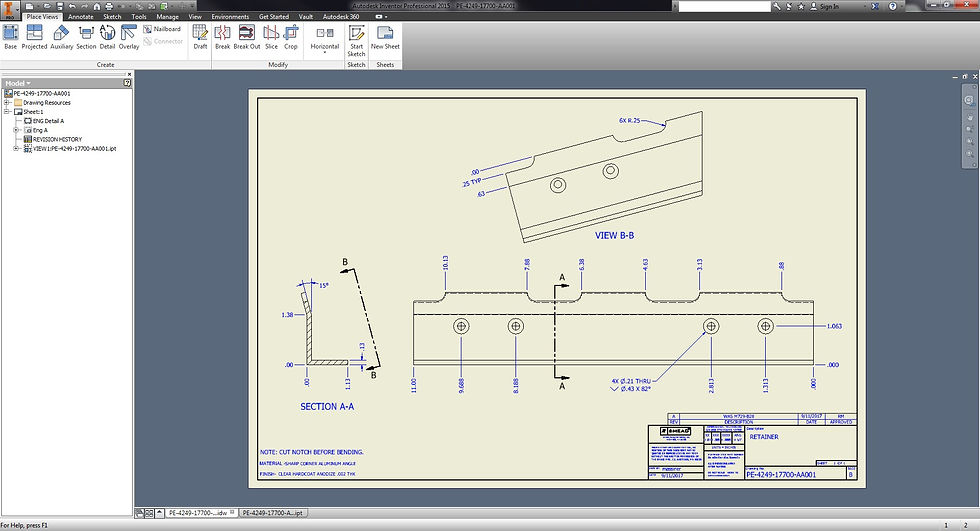

This was a retainer that had a left hand and a mirrored right hand piece. Someone made the suggestion to redesign the parts so the backups could be universal to replace whichever piece broke. This would reduce the number of backups that needed to be stored. My task on this project was to make that happen. The model and the second drawing depict my adjustments to the first drawing.


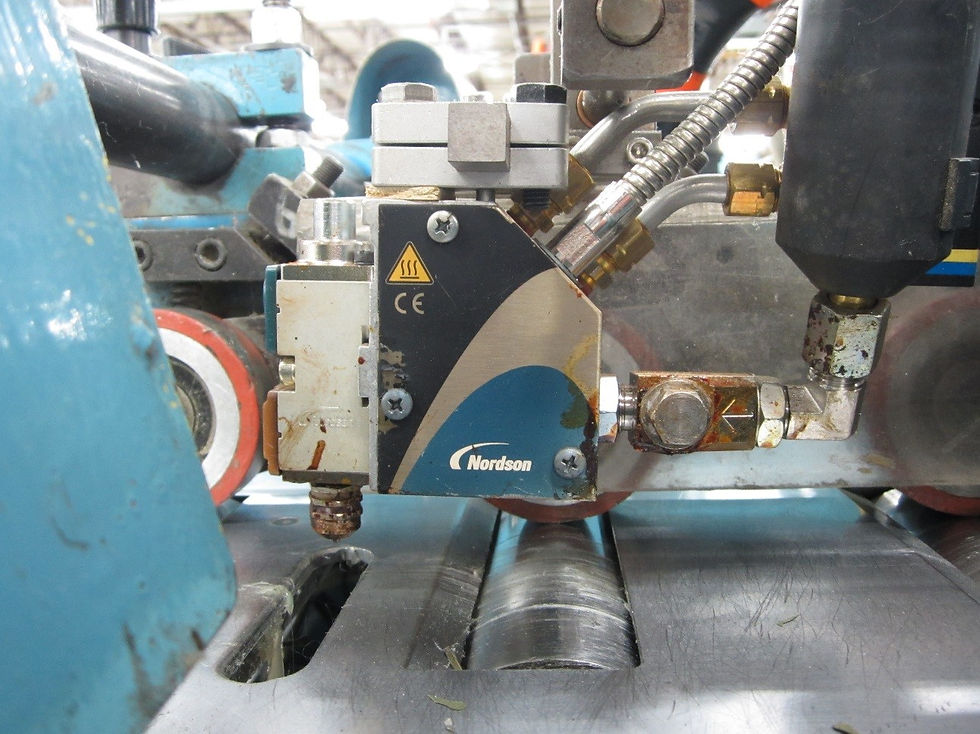

This was my first project at my internship. We upgraded the glue dispensing nozzles on a few of our machines. The problem was they were not compatible with the machines. My job was to create a mount that would allow for adjustments along the X and Z axes. This was the first time I had to model with the manufacturing processes needed to create the parts in mind.
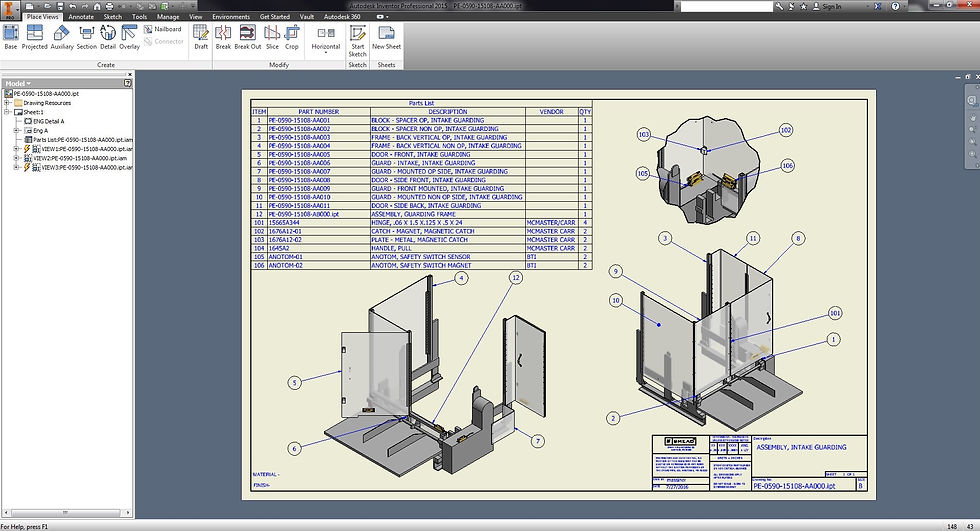
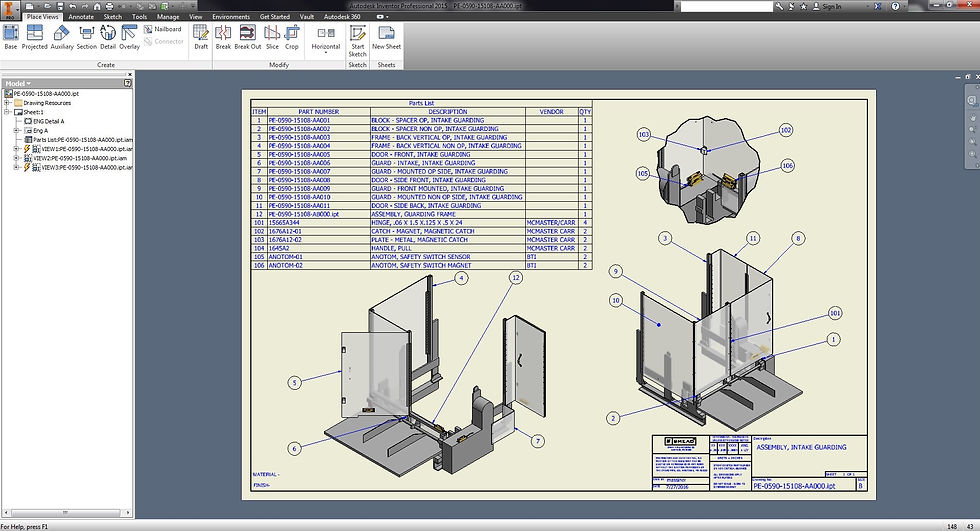
This guarding project was long overdue as the guarding that was being replaced was extremely outdated. This was also a purchased machine from another company and did not come with any drawings. In order to design the guarding around the machine I first had to measure every feature with high accuracy. The folding guarding was needed to allow access from the corner for routine cleaning and maintenance by the machine operators.

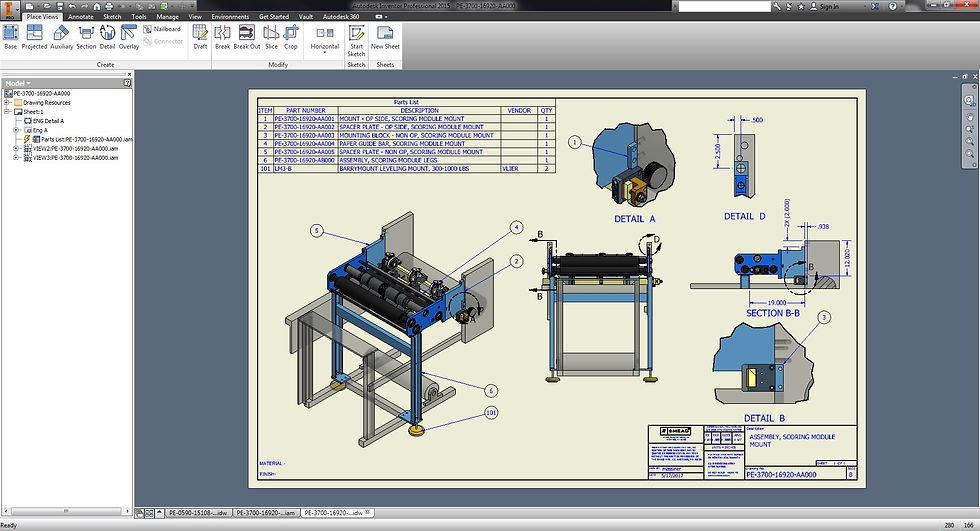
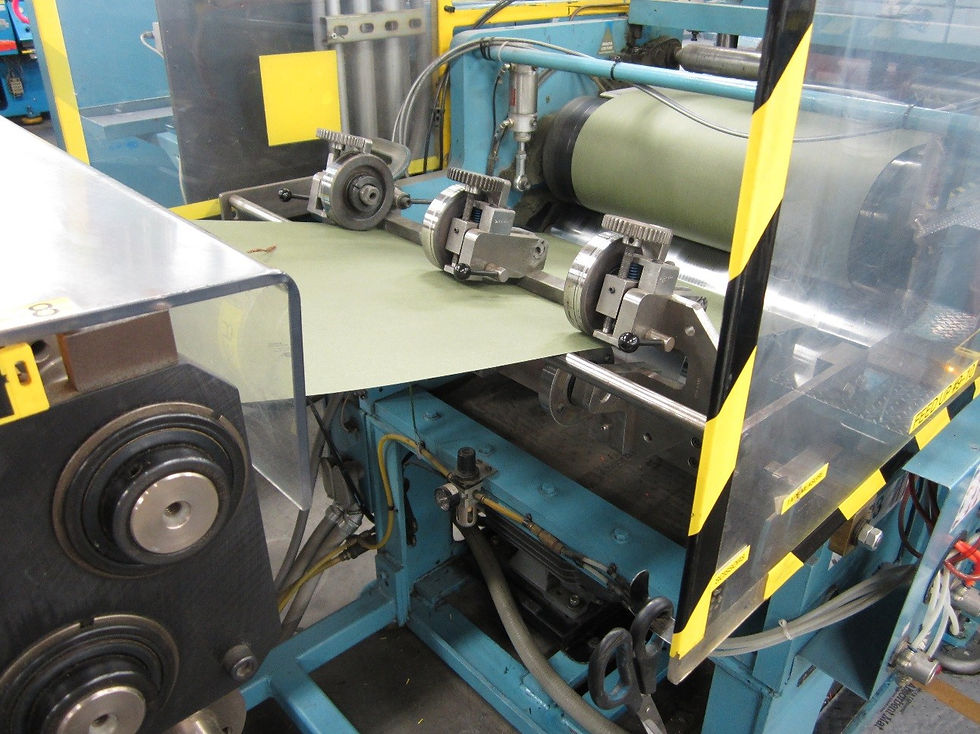

This was a project that involved relocating a section of one of the machines to another. An entirely new mounting system was required as it was being placed between two existing, adjacent sections. The location of the section being moved required a lot of pieces being aligned with high precision.
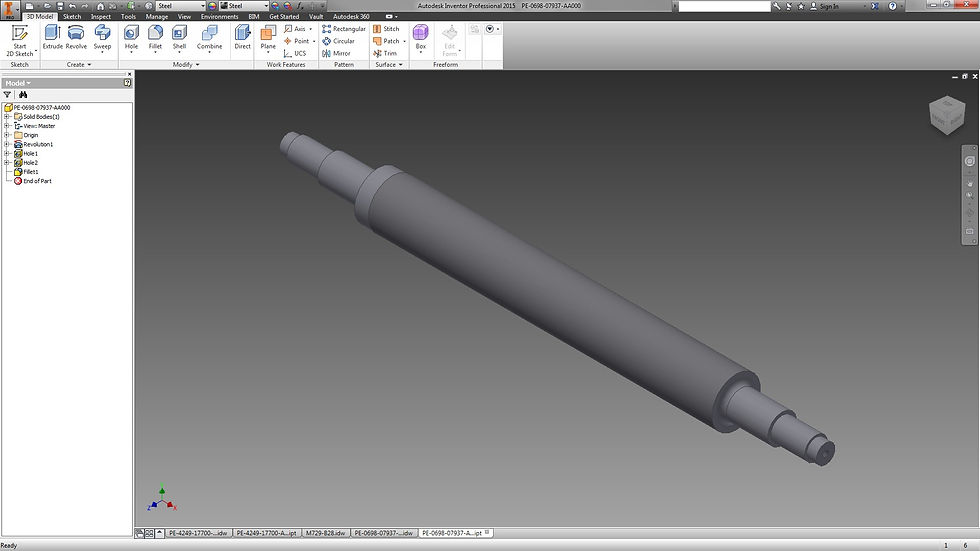
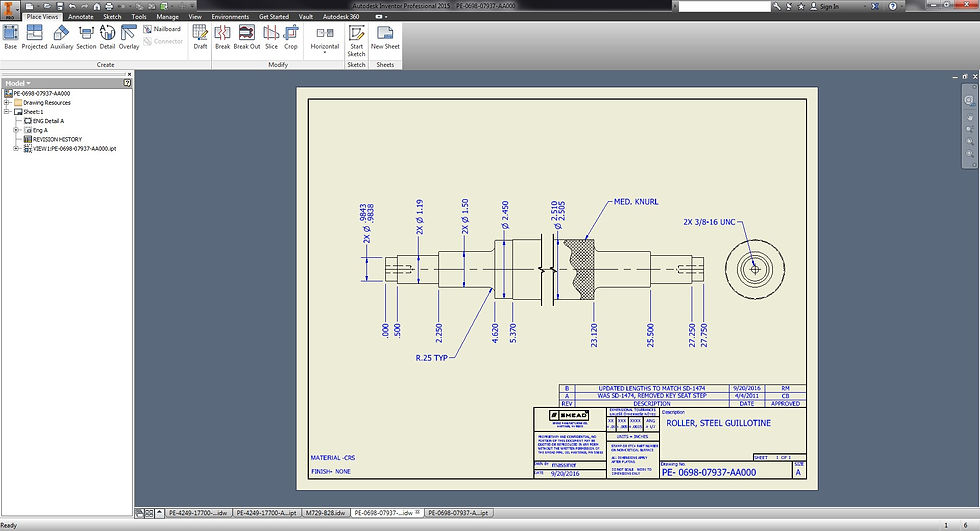

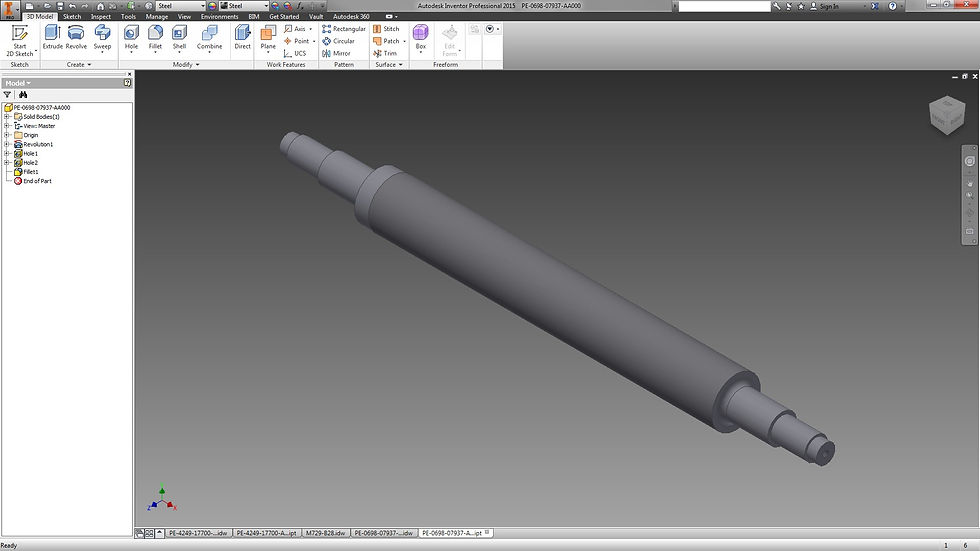
This was the most time consuming project I participated in. We had an area of the plant designated for replacement parts. The largest section in this area was filled with rollers as shown to the right. Over time, rollers were shuffled around and placed in the wrong locations without any form of identification. It was my job to identify the rollers and match them to their corresponding drawings and revision as some had been modified. The drawings were then placed inside the box in their correct locations. The next step is to stamp each roller with it's number.
My largest responsibility involving AutoCAD was updating and maintaining the accuracy of the facility drawing. Any change that was made involving the locations of machinery, updated evacuation plans or any other aspects of the plant needed to be updated by me on a regular basis. Examples of sheets that needed updating are listed in the sheet index.

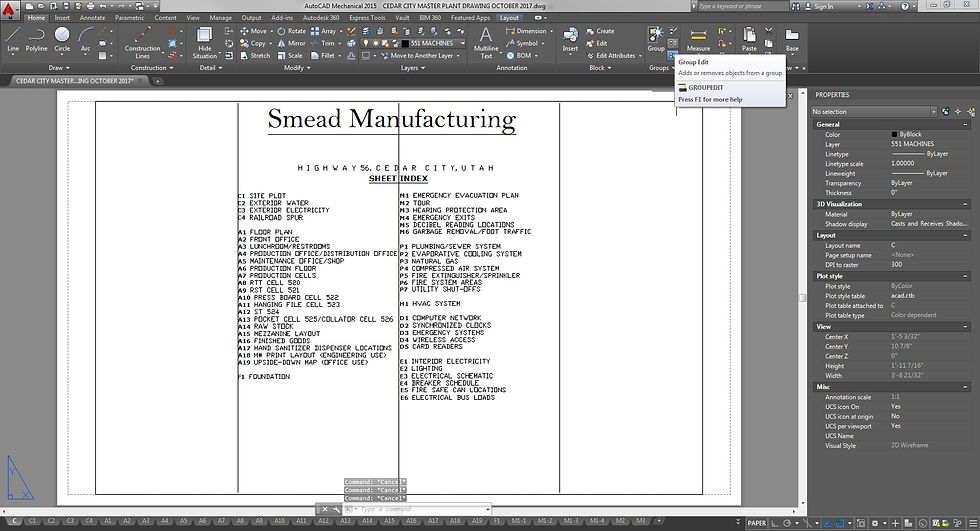



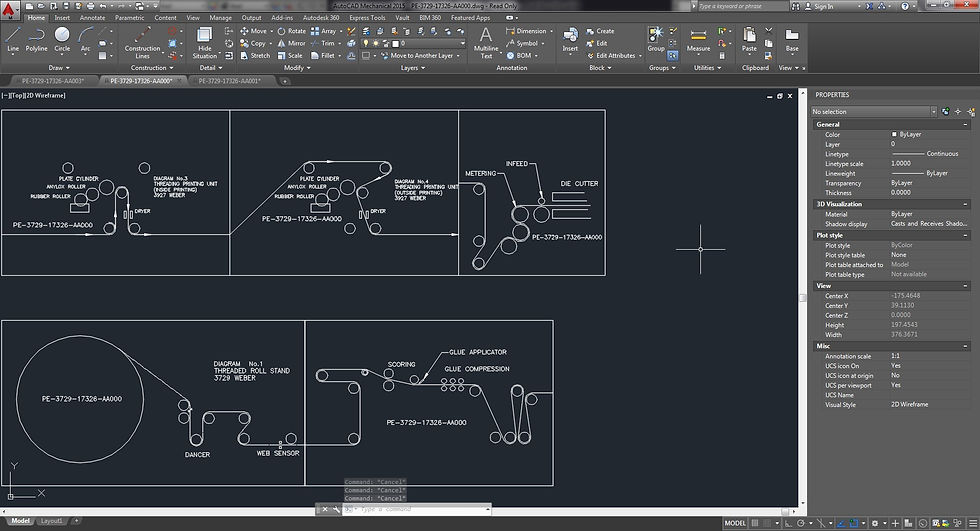

AutoCAD was used occasionally throughout my internship. It was used mostly to create diagrams or labels for quality control tools. Like most other plants there was a period of time before 3D modeling was available. There were a large amount of drawings done in AutoCAD as a result. Whenever I came across one of these drawings I would create a 3D model and an Inventor drawing to help with the modernization in our plant.
One of the most important skills I picked up during my internship was the ability to cost out each of my projects. This new skill also lead to a method of thinking while designing my projects that involved trying to reduce cost by creating easy to manufacture parts to reduce labor costs as well as using the minimum amount of material needed to accomplish the task.


